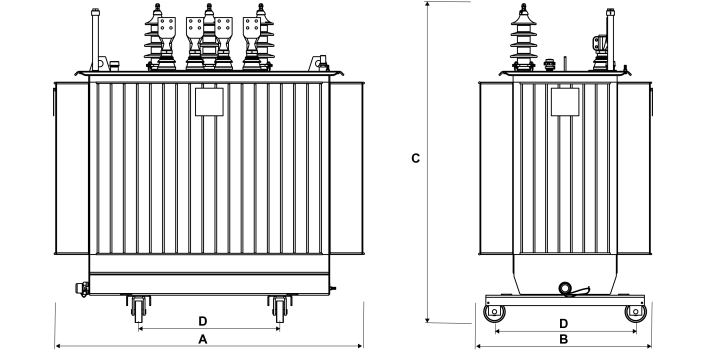
The meticulous and realistic work at the proposal stage eliminates returns in production or design. Our design team gets all the information about the working place and conditions and guides the customer not to make wrong choices.
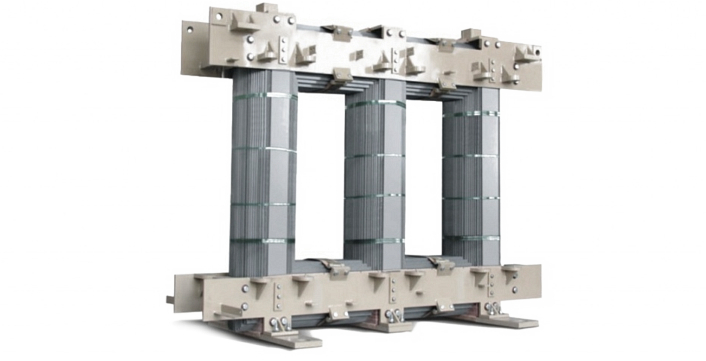
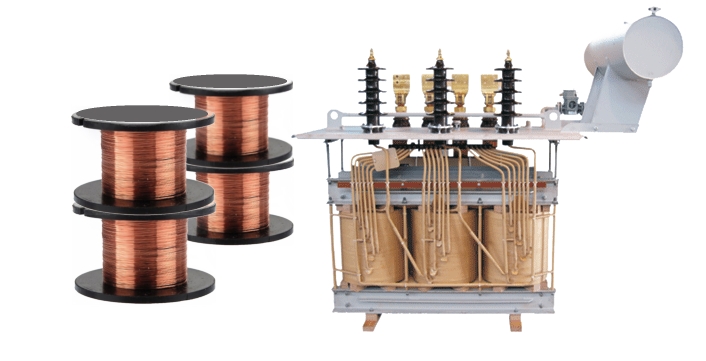
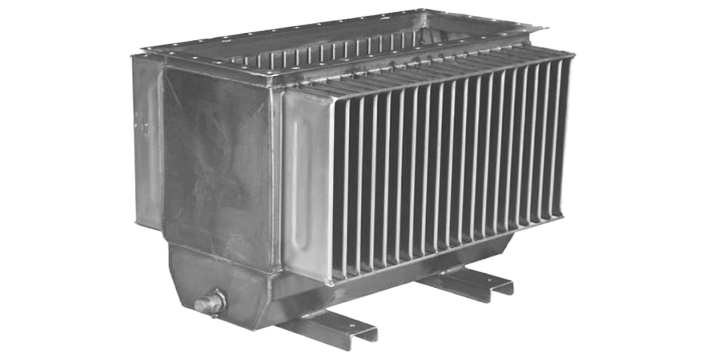
The transformer boiler is manufactured from high quality st-37, st-52, and radiator or elastic wave wall sheets as cooling group. Wave wall and/or radiator sheets are used as 102 mm or 1.5 mm. All equipment is assembled in accordance with the project. Boiler welds are made with a very special impermeable welding technique, due to the welding of thin sheet to thick sheet. After the production of the boiler, the penetrating liquid is squeezed, pressure is applied, and after the leak checks are made in a dark environment with black light, it is shipped to the assembly.
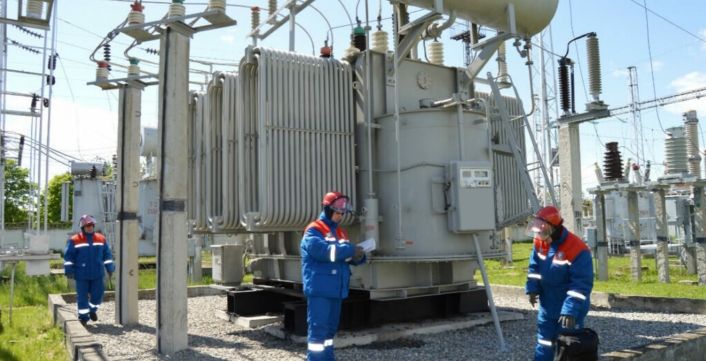
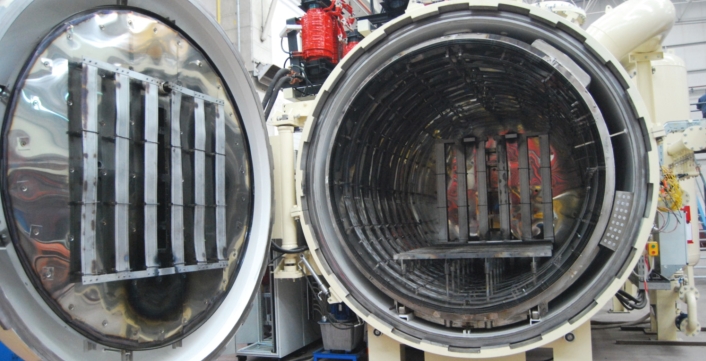
Oil pumping is carried out under high vacuum to transformers that are ovend and boiler mounted. Generally, dehumidified mineral oils are used, which are strengthened in terms of insulation and temperature resistance. In addition, special vegetable or non-combustible oils can also be used.
The process is completed by making oil level adjustments of transformers with expansion tanks and special pressure adjustments of hermetic transformers.